Warehouse and Delivery Management
The Challenge
Toshiba Singapore faced several inefficiencies and delays in their Warehouse and Delivery Management process due to manual interventions and dependency on human effort. The key challenges included:
-
Order Retrieval:
FTEs (Full-Time Employees) manually logged into the orders portal to retrieve order details, which was time-consuming. -
Pick Slip Generation:
FTEs printed Pick Slips to alert warehouse staff for packing items, leading to delays and lack of automation in the process. -
Package Scanning:
FTEs recorded package details like dimensions and weight and completed the scanning process, which added to the processing time. -
Shipment Creation:
FTEs manually created shipments in logistics portals (DHL/UPS) and updated the warehouse application with on-hand stock details. This required constant monitoring and was prone to delays. -
Manual Process Dependency:
The entire process relied heavily on manual input, which was slow, error-prone, and led to operational inefficiencies.
Business Applications: TGCS Web Application, DHL Web Application
RPA Tool: Microsoft Power Automate
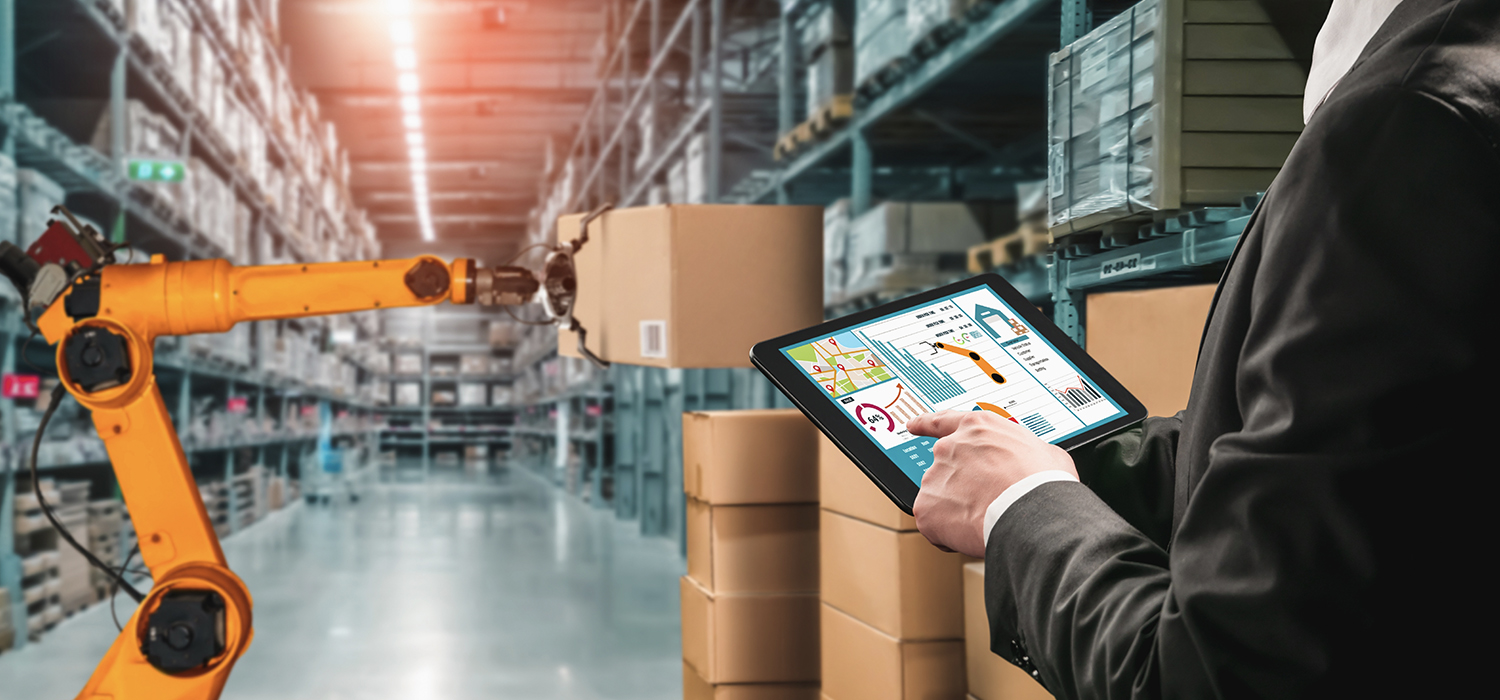
Our Solution
To streamline and optimize the Warehouse and Delivery Management process, we implemented an RPA-based automated solution:
Scheduled Automation
- Bots automatically logged into the orders portal every 10 minutes during shift hours to retrieve order details.
- Bots printed Pick Slips, Invoices, Delivery Orders (DO), and Overpack details for warehouse staff, eliminating the need for manual intervention.
- Bots extracted dimensions and weight details from the scanning portal.
- Shipments were automatically created in DHL/UPS portals, and waybills were printed for each package, ensuring faster processing.
- Bots updated the warehouse application with accurate on-hand stock details, providing real-time inventory visibility and reducing stock discrepancies.
Benefits Realized
-
Improved Efficiency:
Automation eliminated manual tasks, ensuring seamless warehouse and delivery management with minimal human effort. -
3 FTE ROI Achieved:
Significant reduction in staffing requirements while maintaining operational excellence, resulting in a quick return on investment. -
Enhanced Accuracy:
Automation minimized errors in order processing, scanning, and shipment creation, ensuring consistent and error-free operations. -
Faster Turnaround:
Automated workflows led to quicker order processing and package delivery, reducing lead times and improving customer satisfaction. -
Scalable Solution:
The solution is easily adaptable to increased order volumes, allowing the warehouse operations to scale up with minimal adjustments and overhead costs.